Motor Selection
Electric motors are integral to a lot of what we do at Watney, and choosing the right one is essential.
In general, motors come in brushed and brushless form, with brushless motor sub-divided into inner and outer rotor motors, and further into sensored and sensorless, which describe the two distinct methods by which the controller reads the rotor position. Stepper motors are a specific type of brushless motors whose shaft can be rotated with supreme and repeatable accuracy. Steppers are usually used in actuator applications.
TYPE |
ADVANTAGES |
DISADVANTAGES |
![]() Brushed |
|
|
![]() Brushless inner-rotor |
|
|
![]() Brushless outer-rotor |
|
|
![]() Stepper Motor |
|
|
The main questions that define motor selection are…
Does the life requirement allow for a brushed motor?
Typically a brushed motor will last hundreds or even thousands of hours if properly specified, and if power-density allows. If so, this is likely to be the cheapest option because the motor itself will be cheaper than an equivalent brushless motor, and if the application needs one at all, the controller too is simpler and cheaper.
Does the application need a drive?
Usually the output of the motor is too fast and must be reduced through a gear or belt drive, or similar. After motor brushes, the drive is the next item with a measurably finite life. It also adds cost, noise and inefficiency to the assembly.
Do you need support in specifying a motor?
Motor Dyno
Motors are usually advertised by a peak or “rated” power, but these are almost meaningless. The next step after defining a requirement is to work back from a motor’s dyno plot, which is produced for a given supply voltage at all levels of load.
The dyno can be adjusted through re-winding a motor, or changing its magnets, or even its wiring – for example a star to delta configuration in a brushless motor.
Does not apply to stepper motors.
Motor Mounting & Shaft Detail
While we endeavour to always work within an existing motor platform offered by our suppliers, there are adjustments we can make to the motor’s design. Usually we have freedom to specify shaft detail to the specific application, or sometimes even to change the motor mounts if they are post-machined.
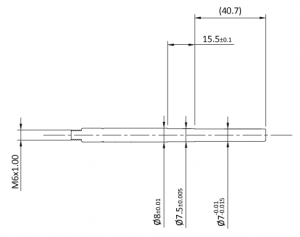
Cooling
No motor is perfectly efficient. Through the dyno curves, the heat output of the motor at any load point can be established and designed for. Some motors are designed to cool themselves via an internal fan (the hot vents on the side of a power tool for example). Others require a flow of cold air applied to them. Others still can be configured with liquid cooling. The product must be designed with motor cooling in mind and Watney can guide this process to ensure it is optimised.
Get in touch
Choosing a motor from a catalogue is one thing, but if you want a production-ready motor that’s properly integral to your product, performs correctly under all circumstances and survives the required life, please get in touch.
Supplier Contacts
At Watney, we have working relationships with some of the world’s biggest motor manufacturers…
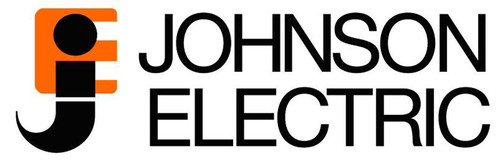
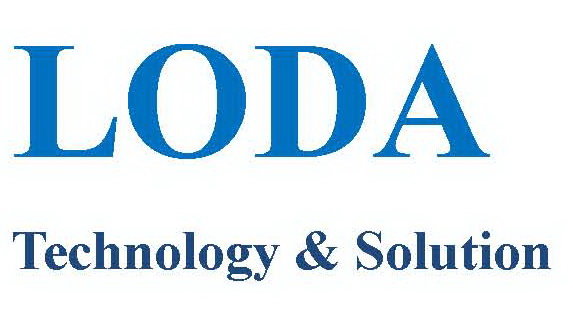
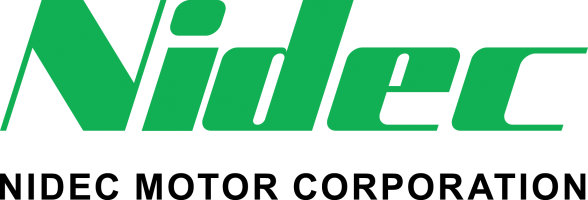

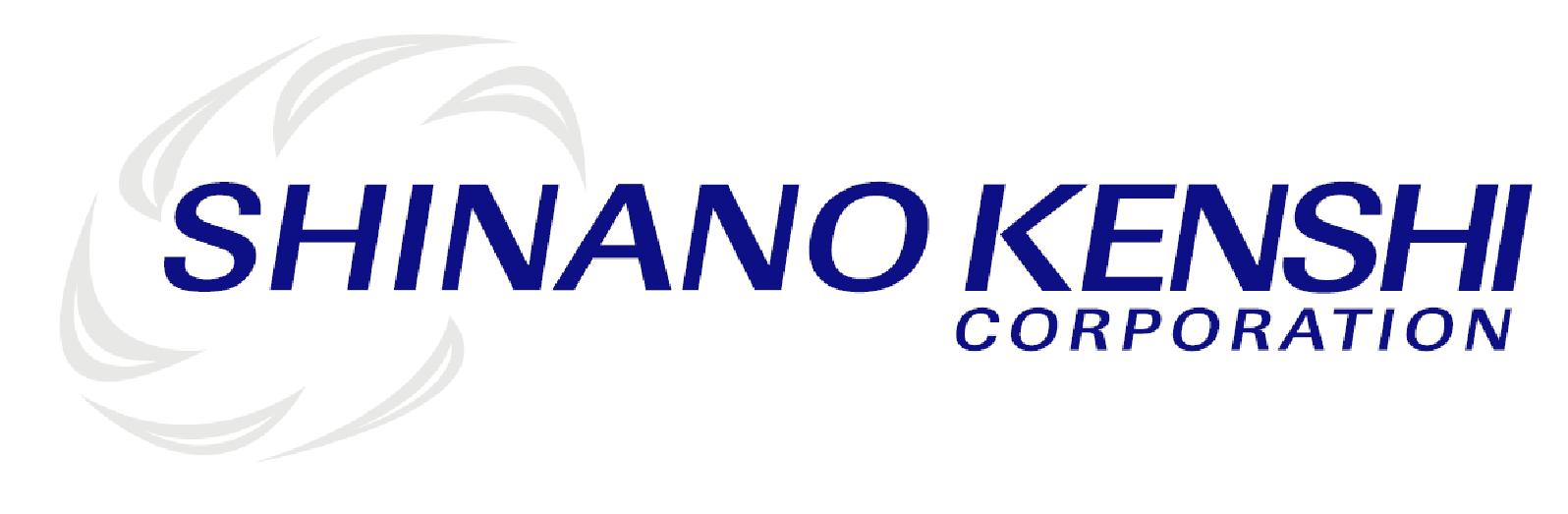
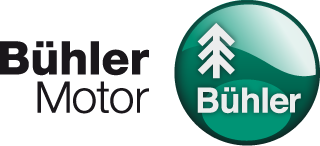
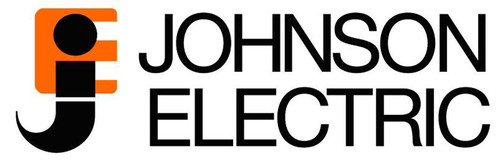
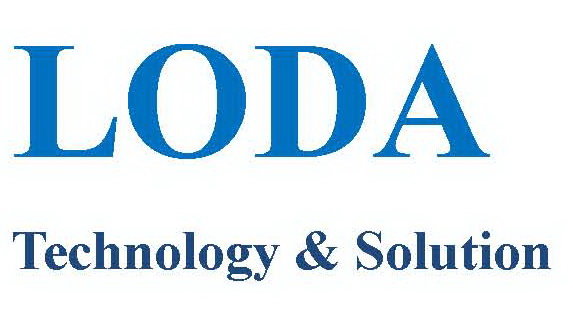
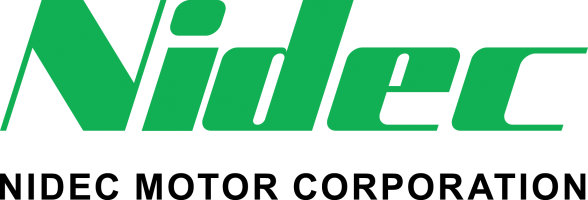

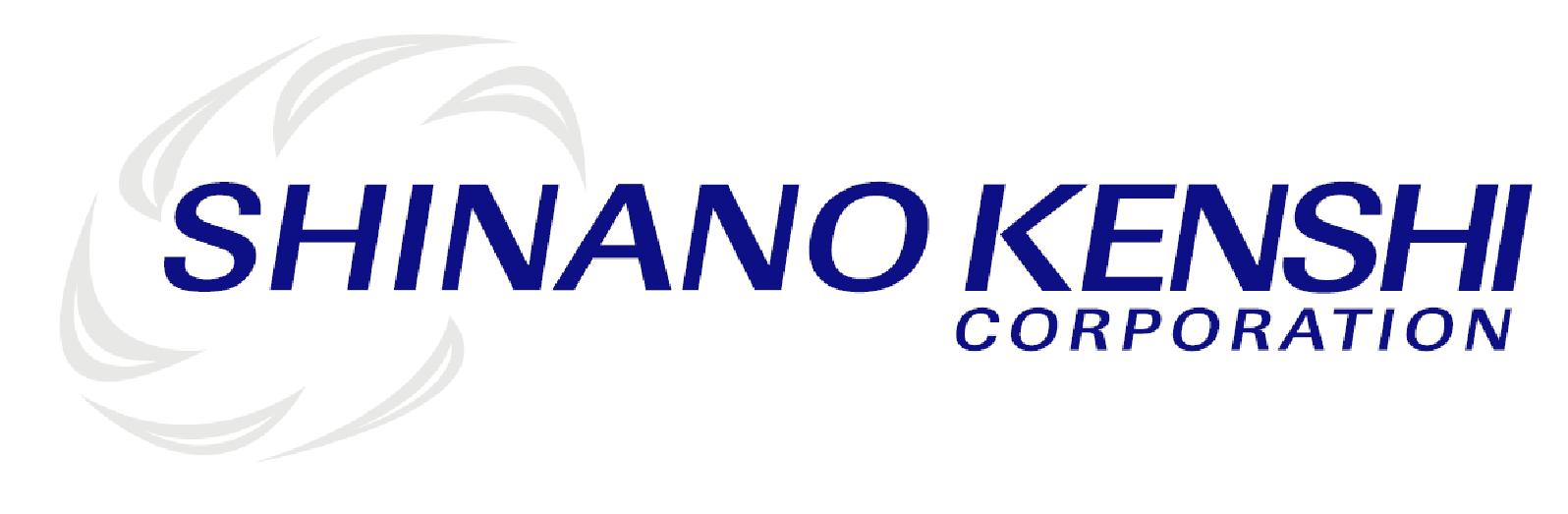
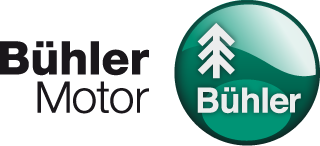